Multiple Amp Heads - Live In
Multiple Amp Heads - Live In
Standard Features
Standard Features
Design: Custom sized to fit your amp heads. This is not a generic "one size fits most" case.
Handles: Recessed handles are used on all of our cases.
Latches: Recessed latches are used on all of our cases.
Corners: Ball corners are used on these cases in order to take the brunt of the abuse and protect the actual case.
Casters: Four 3.5" casters (non-locking) are used on all of our cases. Four 4" casters (each rated at 450 pounds) can be used on cases that are deeper. Stacking caster cups can be added. All cases come with a full length 3/4" Baltic Birch caster pallet.
Foam: Black polyethylene foam is used throughout the case. Typically, 1" foam is used on the sides and the top. 2" foam is used on the bottom because this area tends to take the most abuse.
Foam Floater: A foam floater is a piece of Finnish Birch plywood (with a black phenolic resin exterior) that sits on top of the 2" foam. The amp sits on the foam floater preventing the amps feet from sinking into the foam and helping to evenly distribute the weight of the amp.
Case Construction
Case Construction
Material: 3/8" or 1/2" Finnish Birch plywood with black phenolic resin. This 100% Finnish Birch plywood is made specifically to our specifications. The exterior phenolic resin has a “circle grip” pattern compared to the typical “haircell” pattern found on ABS. Unlike ABS, the phenolic resin will never delaminate.
Extrusions: Double angle extrusion is used to join the panels of the case together. It has a channel that the Finnish Birch plywood lives in. This is superior to single angle extrusion which is simply a piece of right angle aluminum that covers the corner. Double angle extrusion makes for a better, stronger and more durable case. Tongue and groove extrusion is used around the edge of the case where the lid meets the body.
Rivets: All of the rivets are backed by steel washers. Without washers, the rivets will eventually loosen and the case can fall apart.
Welding: The tongue and groove extrusions are welded at key joints in order to significantly strengthen the case. This helps to keep lids closing easily despite years of abuse on the road.
CNC / CAD: Every case starts off life as a detailed CAD model before it hits the manufacturing floor. Panels are precisely machined using state of the art CNC technology affording us the ability to consistently provide uniformity and repeatability. Aluminum extrusion lengths are calculated using CAD modeling systems to ensure a proper fit and are cut using digital technology.
Additional Options
Additional Options
- Recessed label dish (perfect for dry-erase PAL labels).
- 2 locking casters.
- Stacking caster cups.
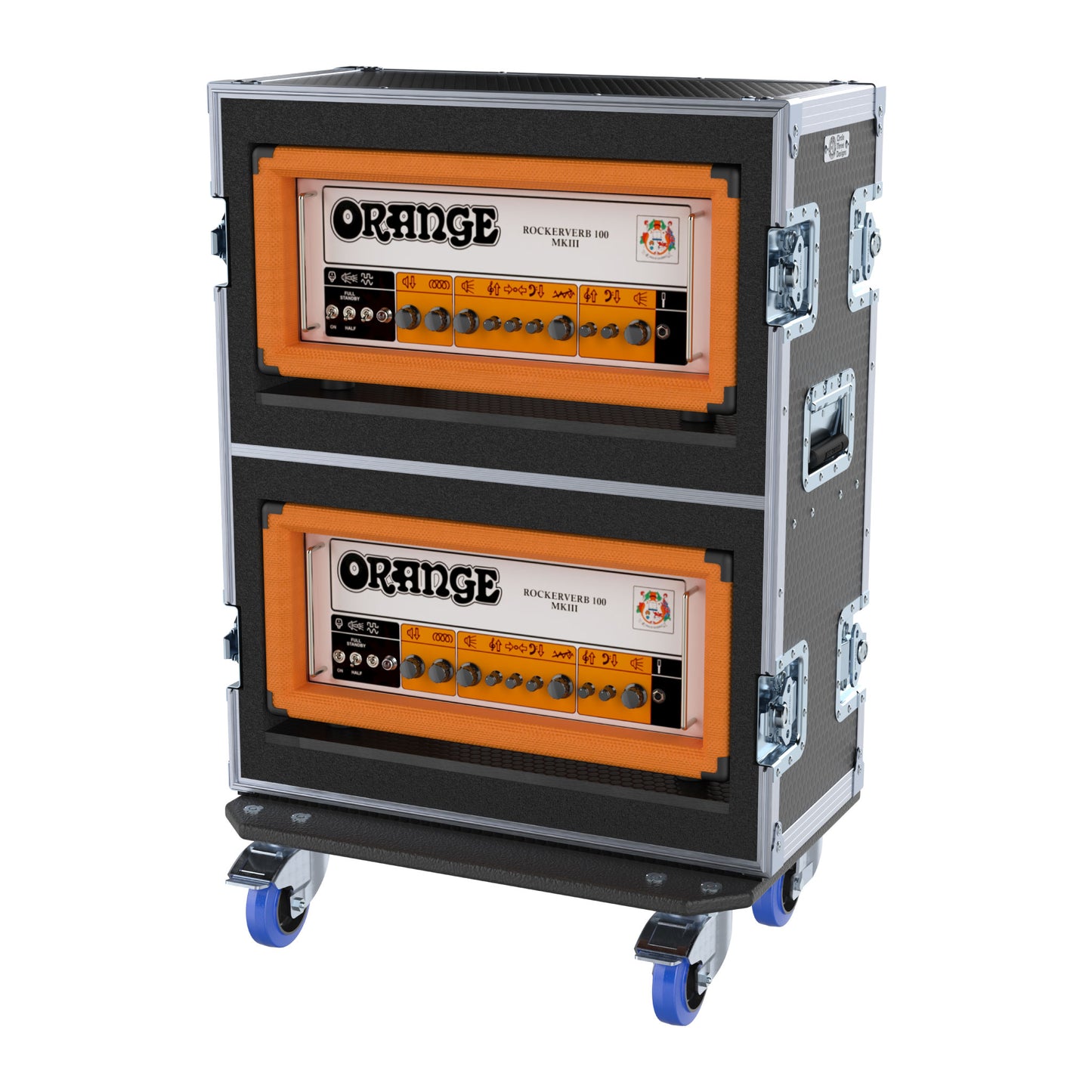
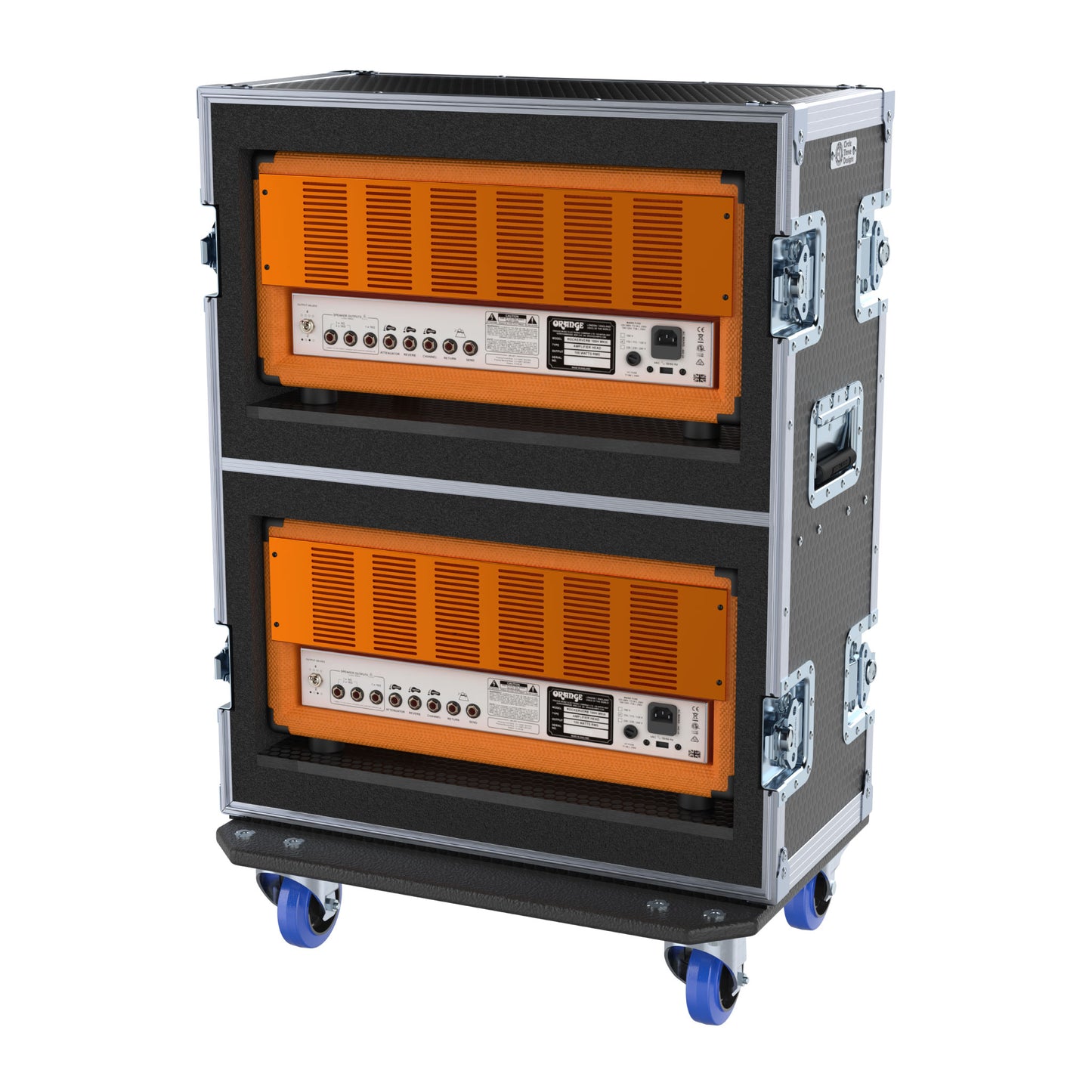
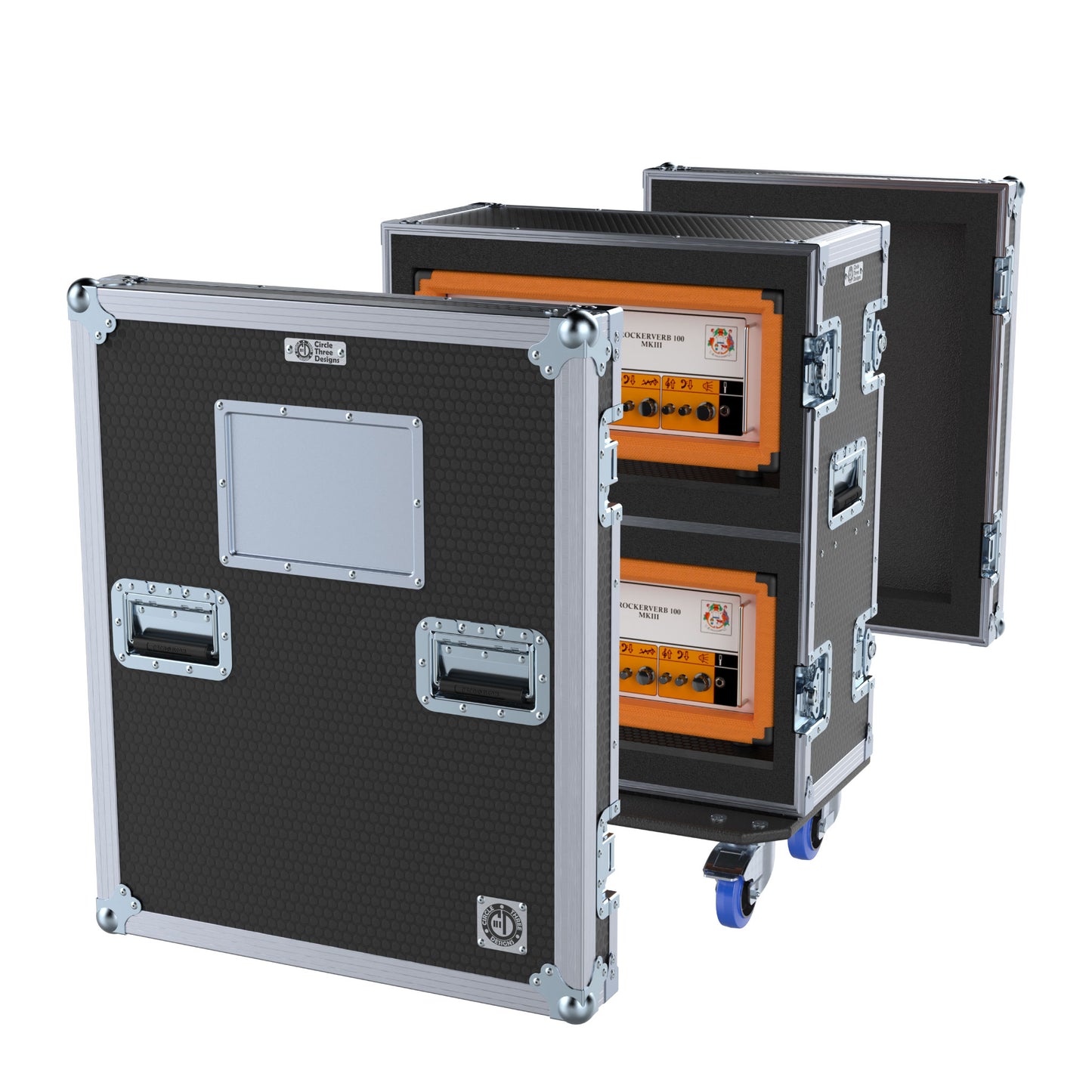

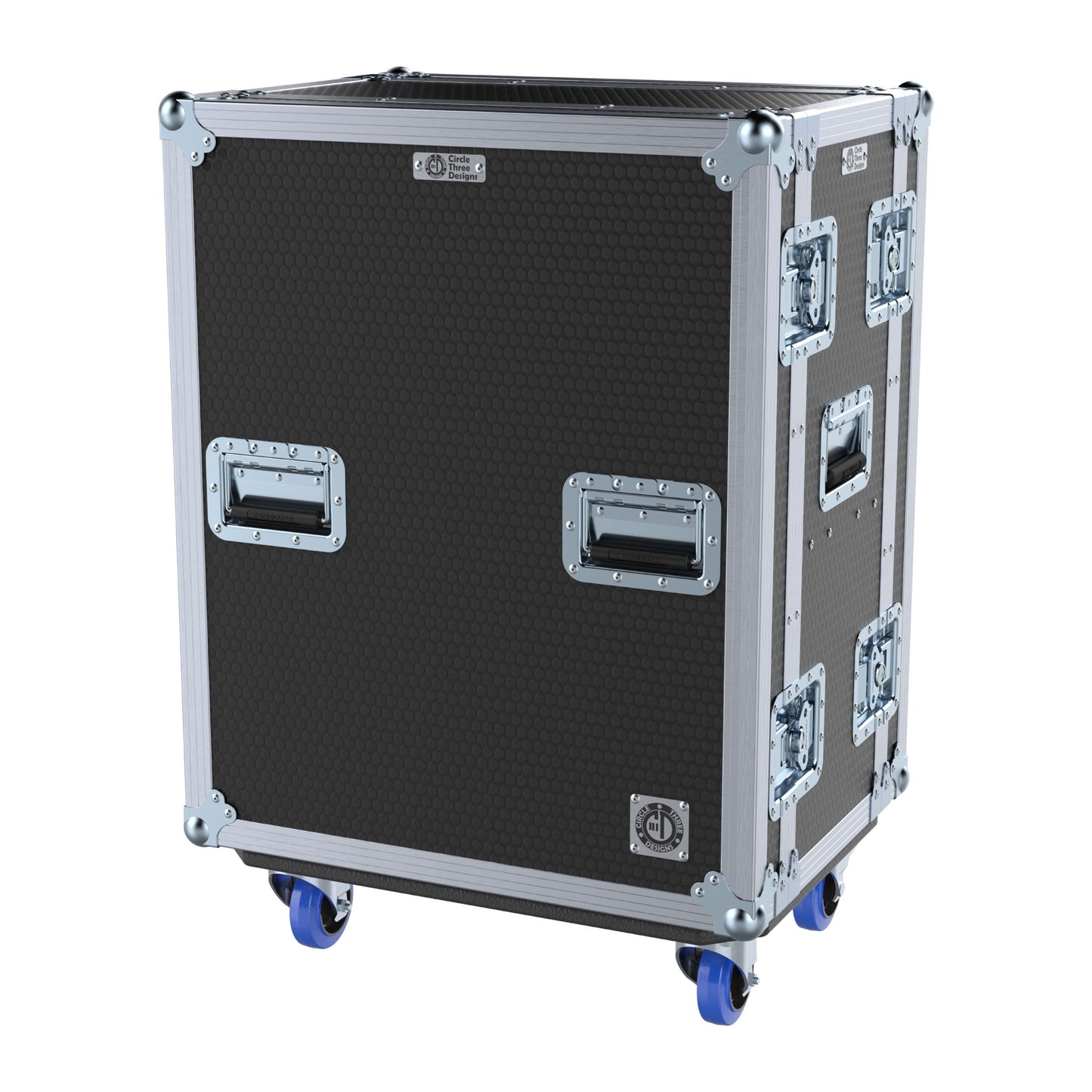
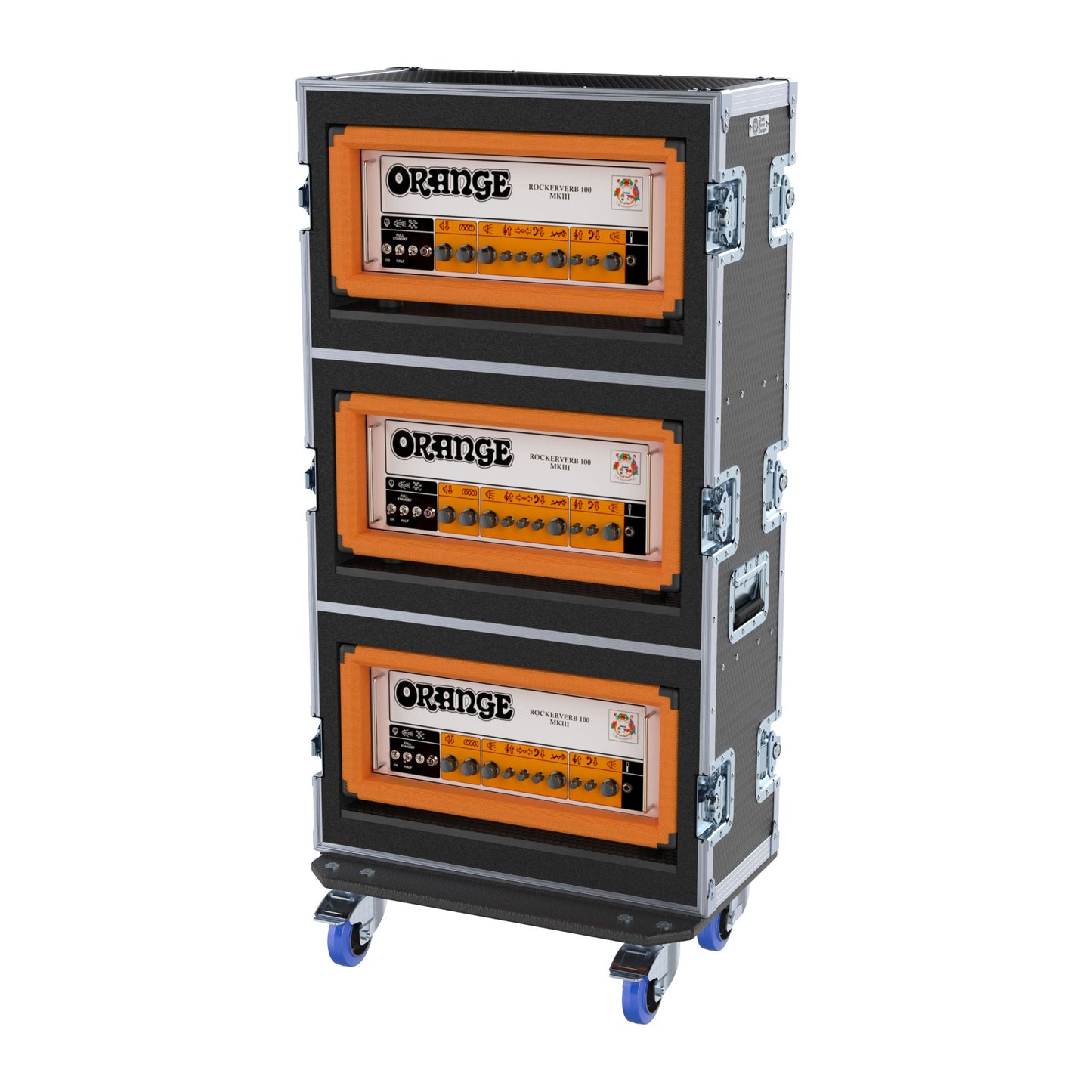
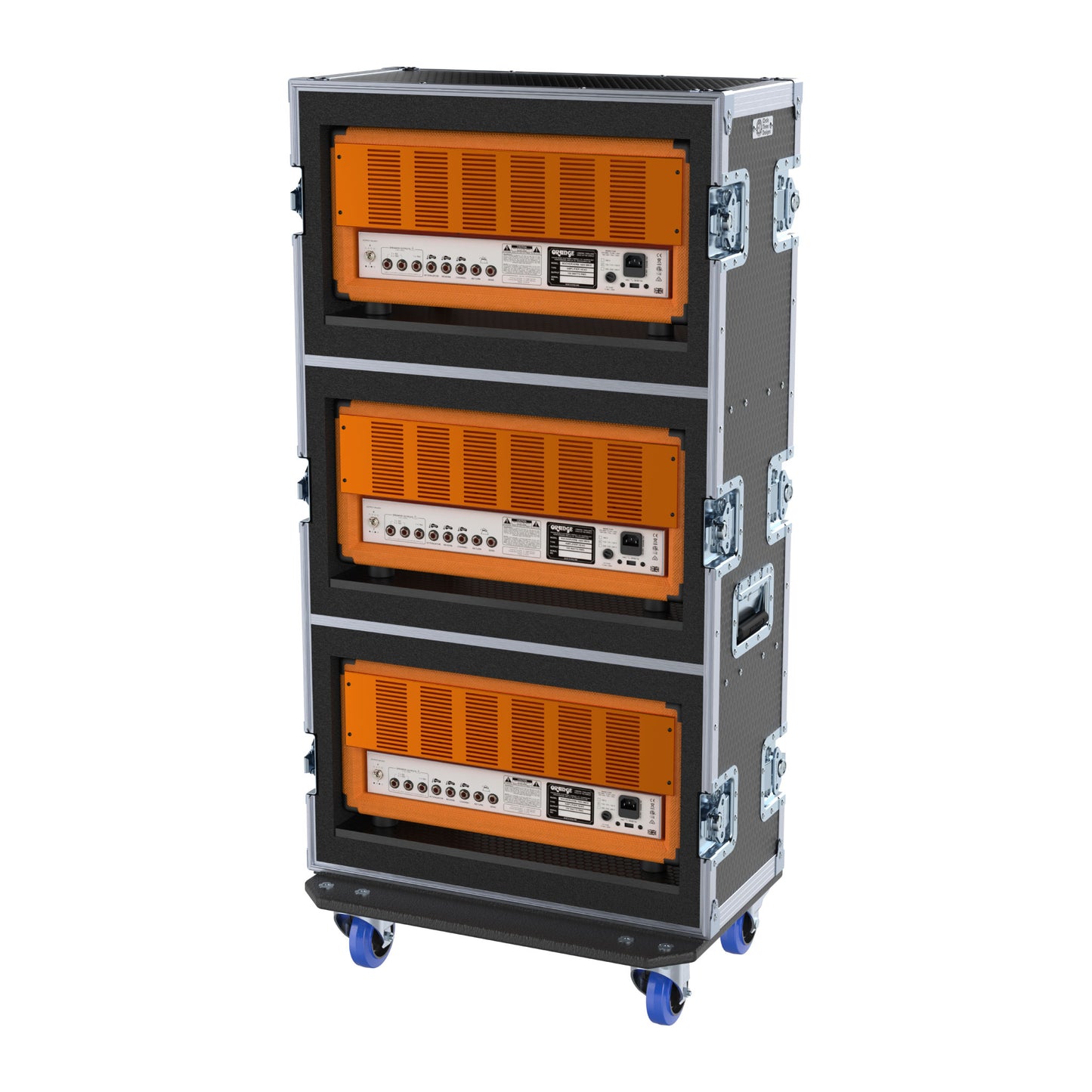
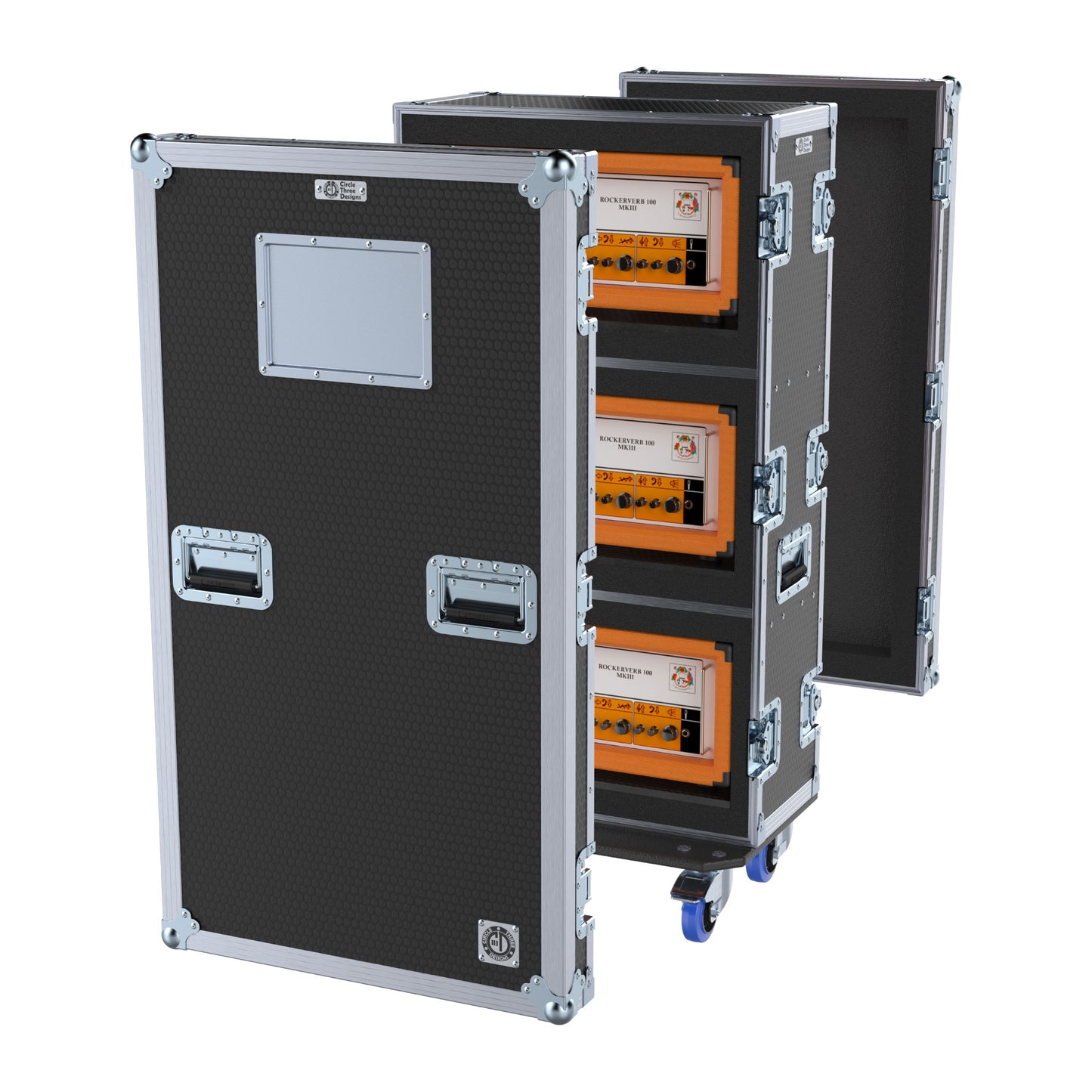
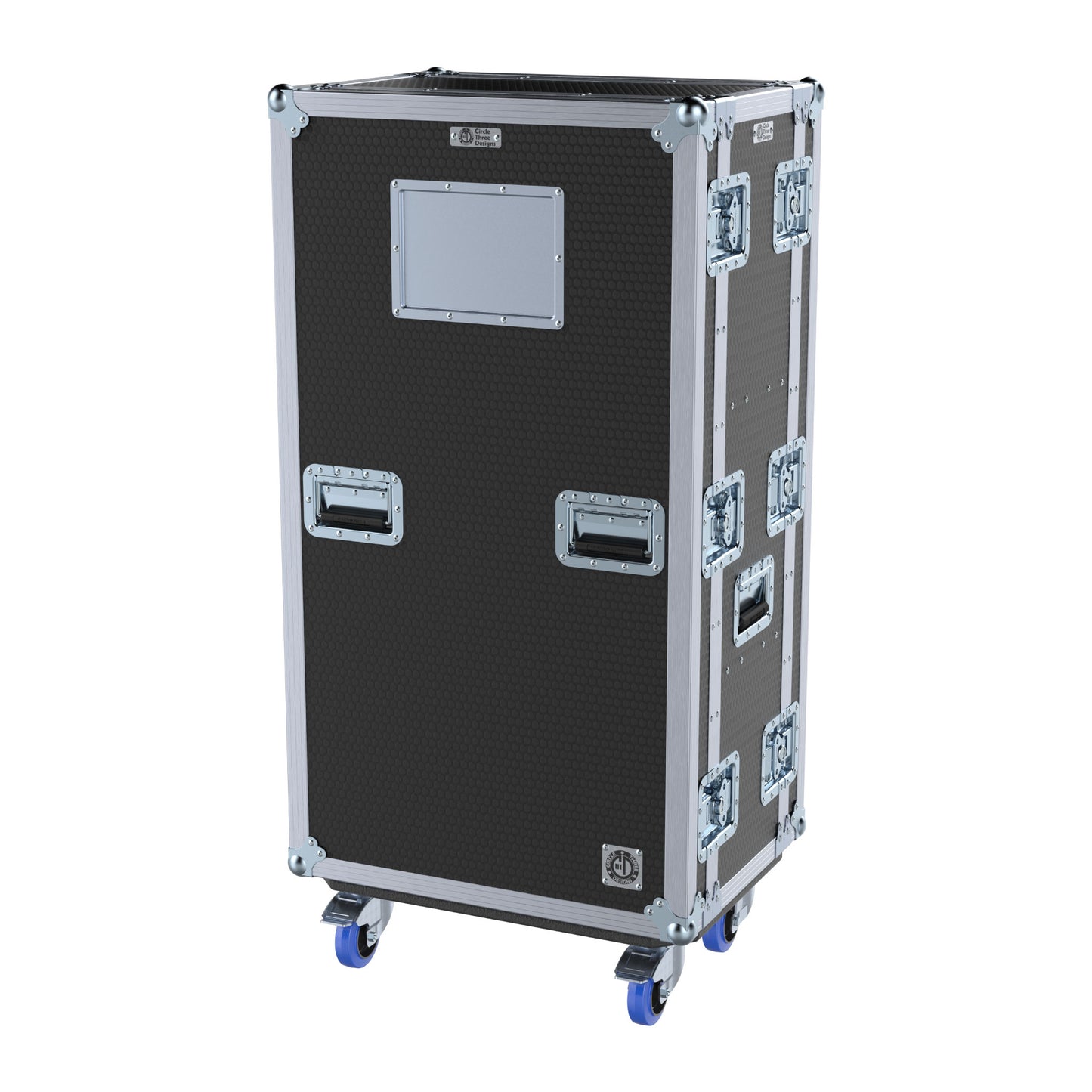
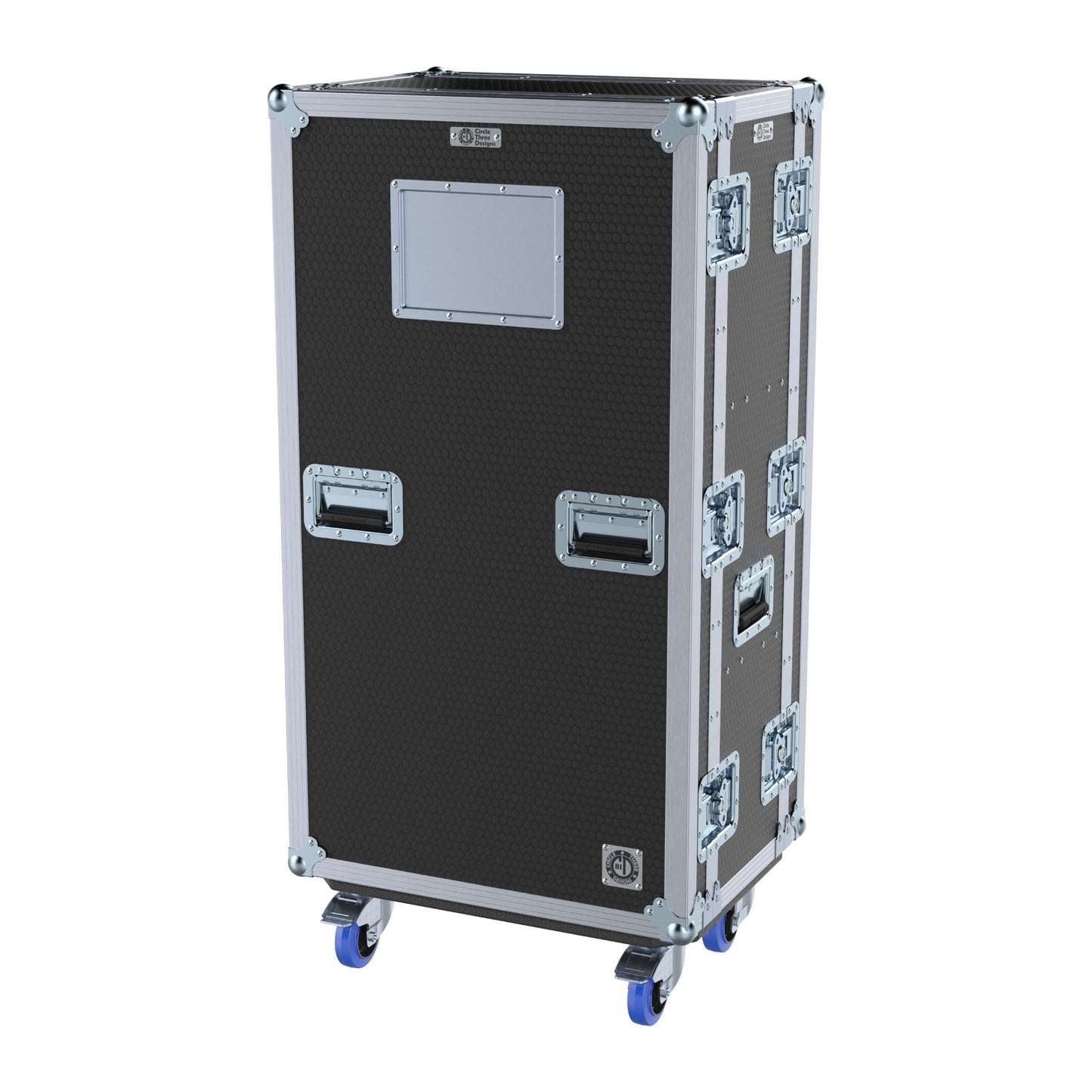
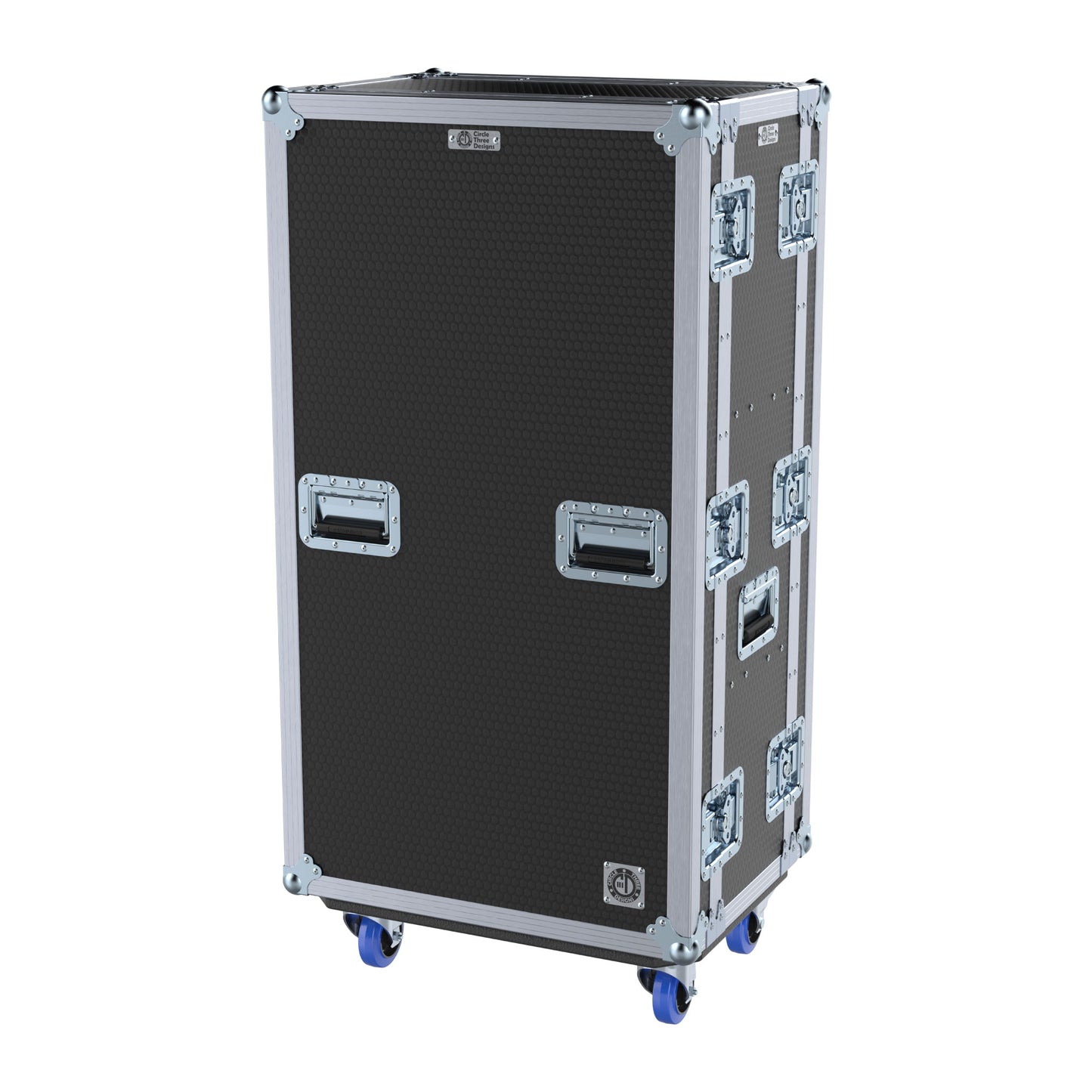